New technologies aren’t just being developed faster than ever — they’re also being adopted faster than ever. Rather few of us could have predicted a couple of years ago that flagship smartphones in 2018 would be putting augmented reality into pockets everywhere.
Manufacturing is one industry that stands to see a huge payoff from the proliferation of AR. There are already lots of compelling use cases out there — many of which could readily apply to even modest companies and job shops. Let’s dive right in.
Why AR for Manufacturing — and Why Now?
Augmented reality occupies a fascinating midpoint on what’s known as the “reality-virtuality continuum.” The phrase is a few decades old, but it has taken a while for the theory to catch up with the technology. Put simply, AR is a technology where virtual objects can be placed in the real environment by combining multiple cameras with display technology that’s “close to the body” — such as a smartphone, a headset or glasses with heads-up capabilities.
In the context of manufacturing, the “reality side” of this continuum is the shop floor or the interior of the manufacturing plant. The “virtuality side” could be any number of digital objects that don’t actually exist in the real world. An exploded view of a lawnmower engine sitting on a workbench, say. Or maybe it’s a portion of an automobile that hasn’t been added yet, or even a proposed modular home component due for construction in a controlled environment.
Substitute whatever it is you build or repair for a living, and you’ll start to see what’s possible here. From training employees on risk-free virtual constructs all the way through to final testing on a complex machine under repair, AR is set to become a vitally important part of safe, efficient and innovative product design, development and fabrication.
Examples Straight From the Manufacturing Industry
This list is by no means a comprehensive one since the list of AR applications seems to grow by the day. Nevertheless, here’s a summary of some of the areas where AR is expected to make an impact:
- Combined with drones, AR lets civic engineers carry out faster and more detailed inspections of infrastructure like dams and bridges.
- AR can connect geographically isolated teams with expert assistance across the world or even out in orbit (more on that shortly). It means people can see with their own eyes what their colleagues are working on and lend detailed, confident assistance.
- Lowering labor costs is a concern for companies everywhere as well as for the democratic structures within those companies, such as unions. If anything, though, AR technology will complement rather than replace human workers. An AR headset could enable a single employee to watch over a significant portion of an automated manufacturing apparatus, but the technology involved would also create new opportunities and positions.
Maybe you already find the idea compelling, but let’s make things a little more (virtually) real with a couple of industry examples already being used today.
1. Simplify or Demystify Complex Assembly Processes
Even the average manufacturing and assembly processes can contain hundreds of individual components. Each of these parts has a specific tolerance, and in many cases, they must be assembled or disassembled in a precise order.
Augmented reality enters the mix by allowing technicians constant access to diagrams, schematics and work orders, right at the periphery of their field of view. Compared with glancing back and forth between the workpiece and, say, a PDF with disassembly instructions, AR glasses are by far a more efficient choice.
With Microsoft’s Dynamics 365 Remote Assistant, for example, workers can easily troubleshoot issues with an expert in real-time. Mixed reality video calling, annotations, and more allow experts to work together with technicians to solve problems.
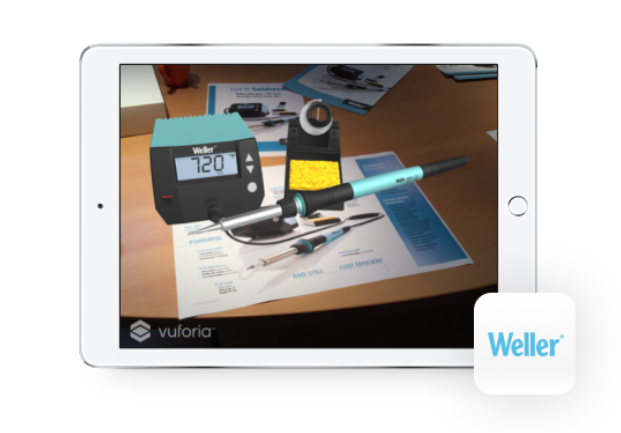
2. “Try Out” Virtual Versions of Real Tools Before You Buy
Not every application of AR technology in the real world is being developed with giant production facilities in mind. Sometimes, all you need to do is see how well a new tool will fit into your workflow or incorporate into your workstation.
With that in mind, Weller Tools is actively adding to their augmented reality iOS app, which lets prospective buyers view the company’s products in a familiar setting: where they carry out their work each day. It’s a great way to get an up-close-and-personal look at the design and footprint of soldering irons and other indispensable tools used by manufacturing facilities and repair centers.
3. Take Advantage of Advanced Training and Troubleshooting Through Fully Visualized Workflows
Lockheed Martin is a pioneer in several fields, including national defense and space exploration. The company has been quick to capitalize on the possibilities of AR gear, including Microsoft’s HoloLens.
Until now, assembling a finished Lockheed F-35 airplane required a time commitment of multiple years. After they applied AR technology to the process, Lockheed engineers dramatically slashed the time required — by up to 30 percent in some cases.
Part of how they accomplished this goal lies in advanced technical instruction through AR, including fully digitized representations of every step in the process, right there in front of the engineer’s eyes. With a gesture or a word, a technician can see which part comes next, where it belongs and what tools they’ll require to get it into place.
For a company with Lockheed’s reach, the possibilities of AR even bring us into outer space. There are times when ground crews and engineering teams might require an extremely detailed view of something occurring on a distant spacecraft. In situations like these, AR might even save lives by allowing remote teams to see exactly what pilots or astronauts are seeing, all in real-time. Leveraging AR tech here means faster resolutions to problems that might otherwise pose a serious threat to human lives.
Manufacturing Is Just Getting Started With AR
Excited yet? You should be. Augmented reality is widely expected to see huge growth over the next couple of years. Not just in manufacturing either, but all across the world and in every industry under the sun. With swift adoption and widespread penetration in multiple verticals, you can expect the cost of entry to fall as well. Even small businesses will be able to carry out maintenance, inspections and assembly with greater speed, accuracy and profitability than ever.